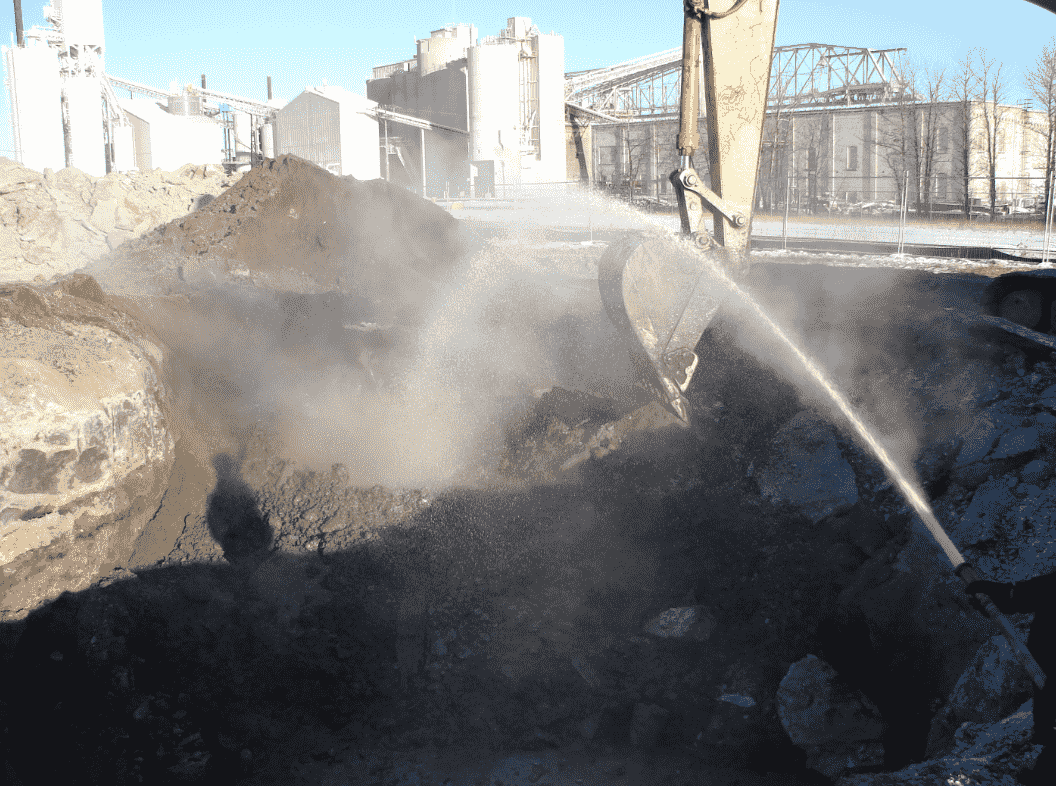
Applications
Pit-Stop™
DTI has developed a process, based upon the Cool-Ox® chemistry, to treat excavations for odor control where large quantities of pollutants are uncovered during the excavation work. This technology has been used to treat several sites and is known to the industry as the Pit-Stop™ Process.
The purpose of the Pit-Stop™ Process is two-fold. The first is to remediate contaminants found during excavation activities and secondly, to eliminate odors caused by the presence of such contaminants.
An explanation of the remedial oxidation mechanism can be found by consulting the Cool-Ox® technology section. Odor control proceeds by an extended mechanism of this process.
A characteristic of the Cool-Ox® Technology is the production of a lather (resembling dirty shaving cream), when the reagent reacts with organic contaminants. This reaction proceeds when any organic compound reacts with hydrogen peroxide derived oxidizers in an in-situ environment but, is useful only when the reaction can be controlled. Hydroxylation of organic molecules produce oxygenated carbonaceous products.
Because these compounds contain both a hydrophobic and hydrophilic component, they are by nature, wetting agents or in the broad sense of the term; surfactants. As such, they produce a foam when agitated. This foam insulates the contaminant (the source of odors) from the air (the transport mechanism) in the excavation thus inhibiting the distribution of the volatile odor compounds.
While this chemo-mechanical system works well to suppress odors, the subtlety of the process is the conversion of the odorous molecules themselves to surfactants. This not only reduces their concentrations but, converts them to more water soluble compounds (surfactants) that in fact, trap them in the reagent rich reaction matrix. Thus, as the reaction proceeds, the volatile compounds responsible for causing odorous conditions are themselves converted to the suppressants that obviate the problem.
This photo depicts Pit-Stop™ being applied to an excavation during backfill activities. The generation of lather indicates that the reagent is reacting with contaminants in the soil and water. When applied prior to backfilling, the agitation of the fill aids in mixing the reagent with contaminants in the soil and water. When applied prior to backfilling, the agitation of the fill aids in mixing the reagent with the contaminants while preventing the fill material from becoming contaminated.
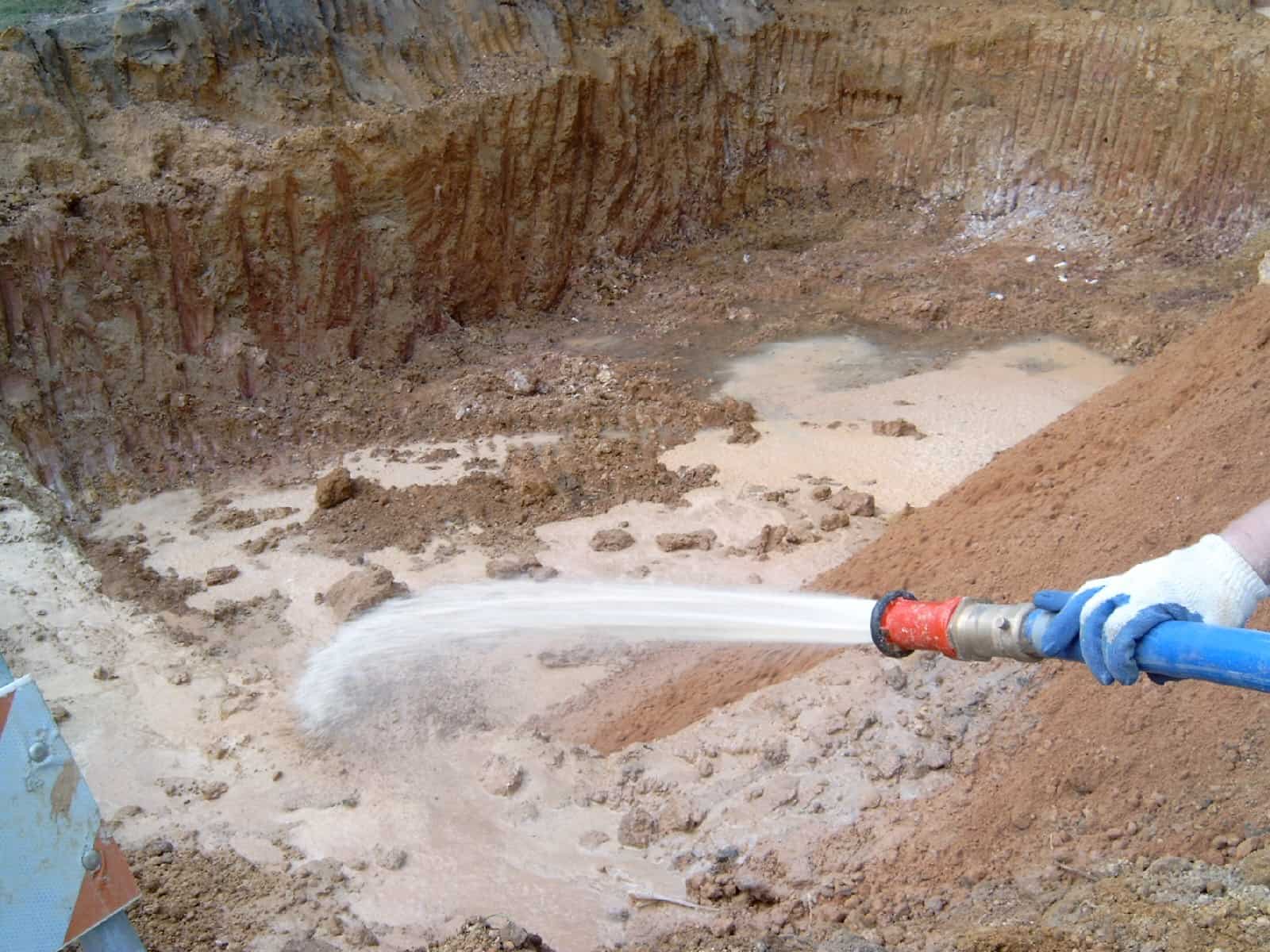
This photo depicts free product starting to react (lighter tan bands) with the Pit-Stop™ reagent. It is very important to note that although a tight lather is formed by the reaction of the oxidizing reagent with the contaminant, no heat is generated. Thus thermal volatilization is obviated.
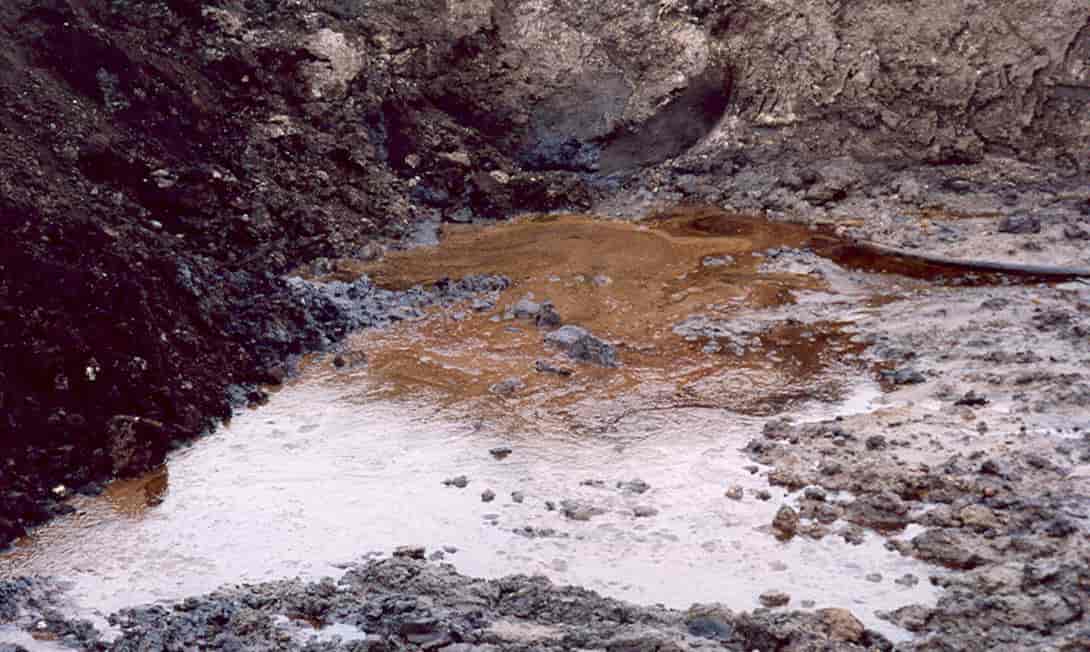
This photo shows free product reacting with Pit-Stop™. Note the heavy lather (tan foam) covering the groundwater thus forming a barrier that prevents the escape of odorous volatile compounds.
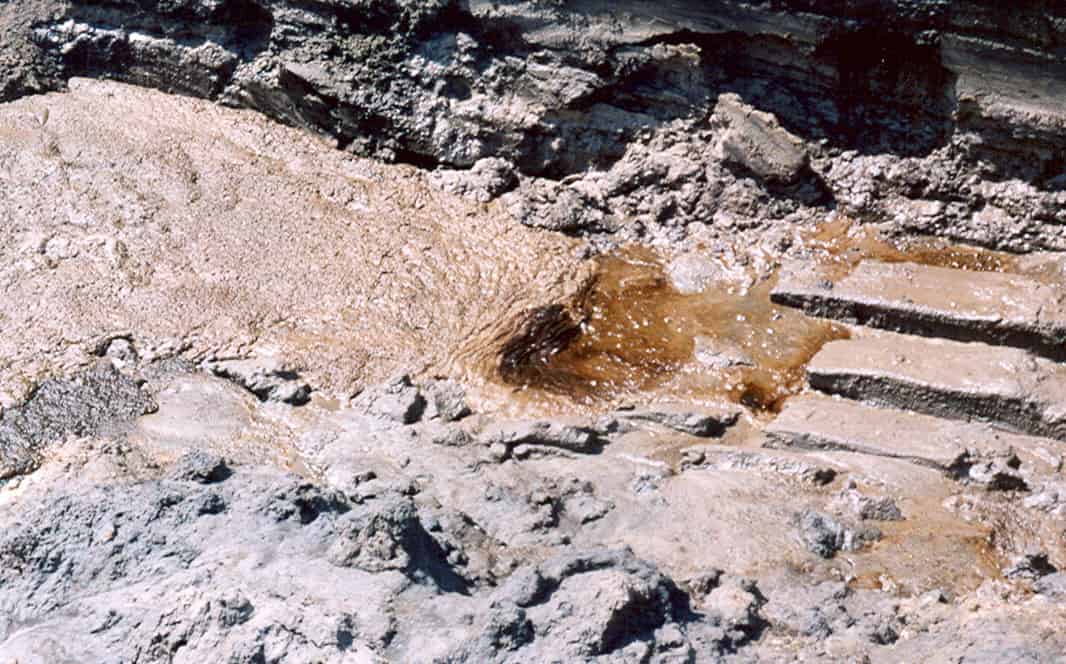
This photo reveals the venous groundwater transport structure found in tight clay. The “white spider web” lines depict the Pit-Stop™ reagent reacting with Diesel Range Organics (DRO) and Gasoline Range Organics (GRO) contaminants in the groundwater leaching from the strata. 97% of DTIs projects have been conducted in clay matrices. This is one of the tracking mechanisms DTI employs to delineate contaminants. Note the foam in the bottom of the excavation.
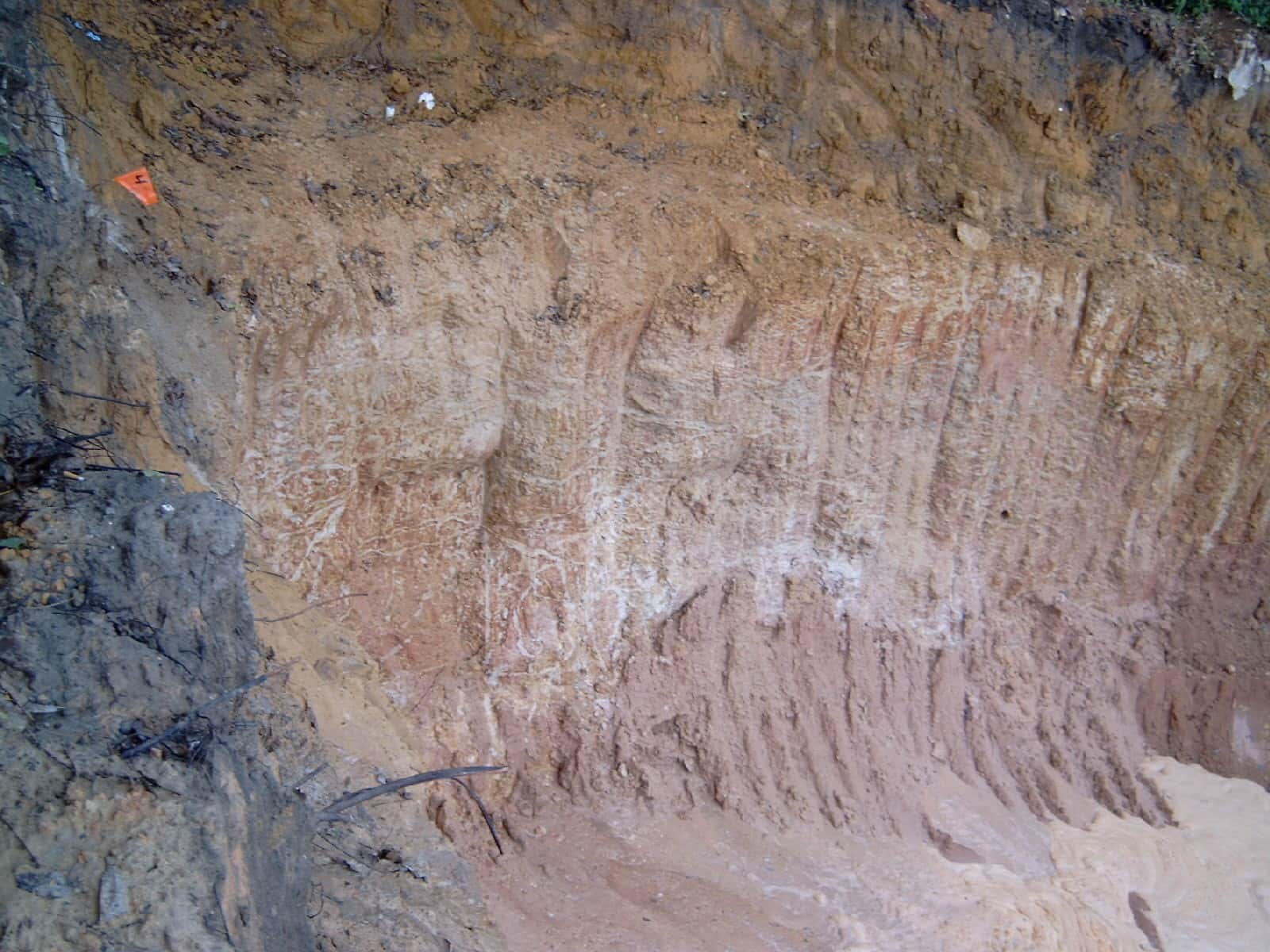
These photos depict free product encountered during excavation activities at a site. Although, nearly the whole excavation contained contaminant concentrations similar to those shown in the photographs, sampling events six (6) months subsequent to the Pit-Stop™ application revealed that the free product had been completely eradicated.