Direct Push Drilling
Destroy Contaminants In Both Soil & Groundwater With The Most Cost-Effective, Efficient DPT Application Process In The Industry
Hire DeepEarth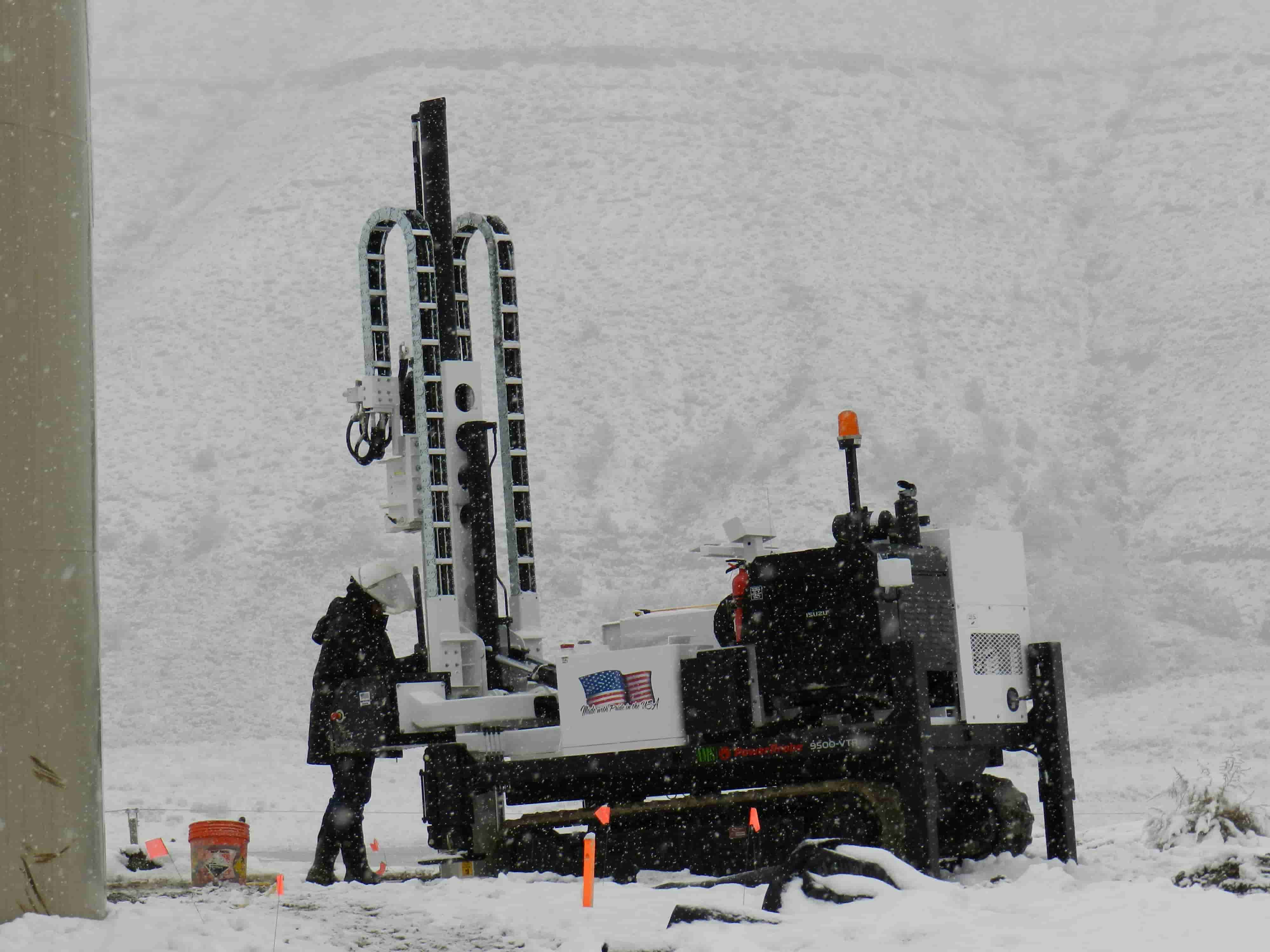
Direct Push Technology
Direct Push (DP) methods allow the sampling, logging, and remediation of contaminants in the subsurface. When these methods are carried out, direct push machines use hydraulic hammers to drive equipment to the desired depth. Regardless of the process - whether sampling, remediating, etc., direct push technology can generally not be used if soil consists of a large amount of limestone, cobbles, granite, or rock.
How Direct Push Differs From Other Drilling Methods
DPT (Direct Push Technology) differs from traditional rotary drilling in that hollow stem augers are used to carry out sampling and treatment instead of rotary drills. This method uses the static weight of the DP machine and the force generated from the hydraulic hammer to bore the hollow stem augers down to the desired depth.
A common issue with the traditional rotary methods is the need to gather and either decontaminate or dispose of drill cuttings. The benefit of DP is that no drill cuttings are generated. However, rotary drilling can reach greater depths than the typical 100 - 120 feet achieved with DP.
Also, DP has more limitations in the types of soils it can bore through. Typically you cannot use DPT where significant concentrations of rock, cobbles, granite, or limestone exist. Here at DeepEarth, we've figured out a way to bypass this to an extent, but even so, sites with large amounts of limestone, cobble, rock, and granite are less feasible with DP.
Direct Push (DP) Machines
DP machines come in various sizes for a variety of remedial situations. They also generally are mounted in one of two distinct ways. Some machines are mounted on tracks, and some are mounted on trucks.
DP rigs come in a variety of sizes. Larger machines are designed to reach greater depths than 100 feet, and smaller ones are designed to fit through man-doors to treat contaminants present through the subfloor - when drilling at an angle isn't an option.
Track Mounted DP Machines
Due to the weight and requirements of these machines, they are typically track-mounted to maneuver through various conditions, from sand, clays, and even snow/ice. These tracks become even more vital as the machine being used is larger because they will often need to position themselves in more specific positions to treat at certain angles and depths. So the ability to maneuver precisely is essential.
Truck Mounted DP Machines
Truck-mounted DP machines can generally do all the same things track-mounted machines can, but they are more limited in mobility. In some conditions, where track-mounted machines can easily reach and treat, truck-mounted machines can not, such as certain sandy and or snowy conditions.
Our Custom DP Machine
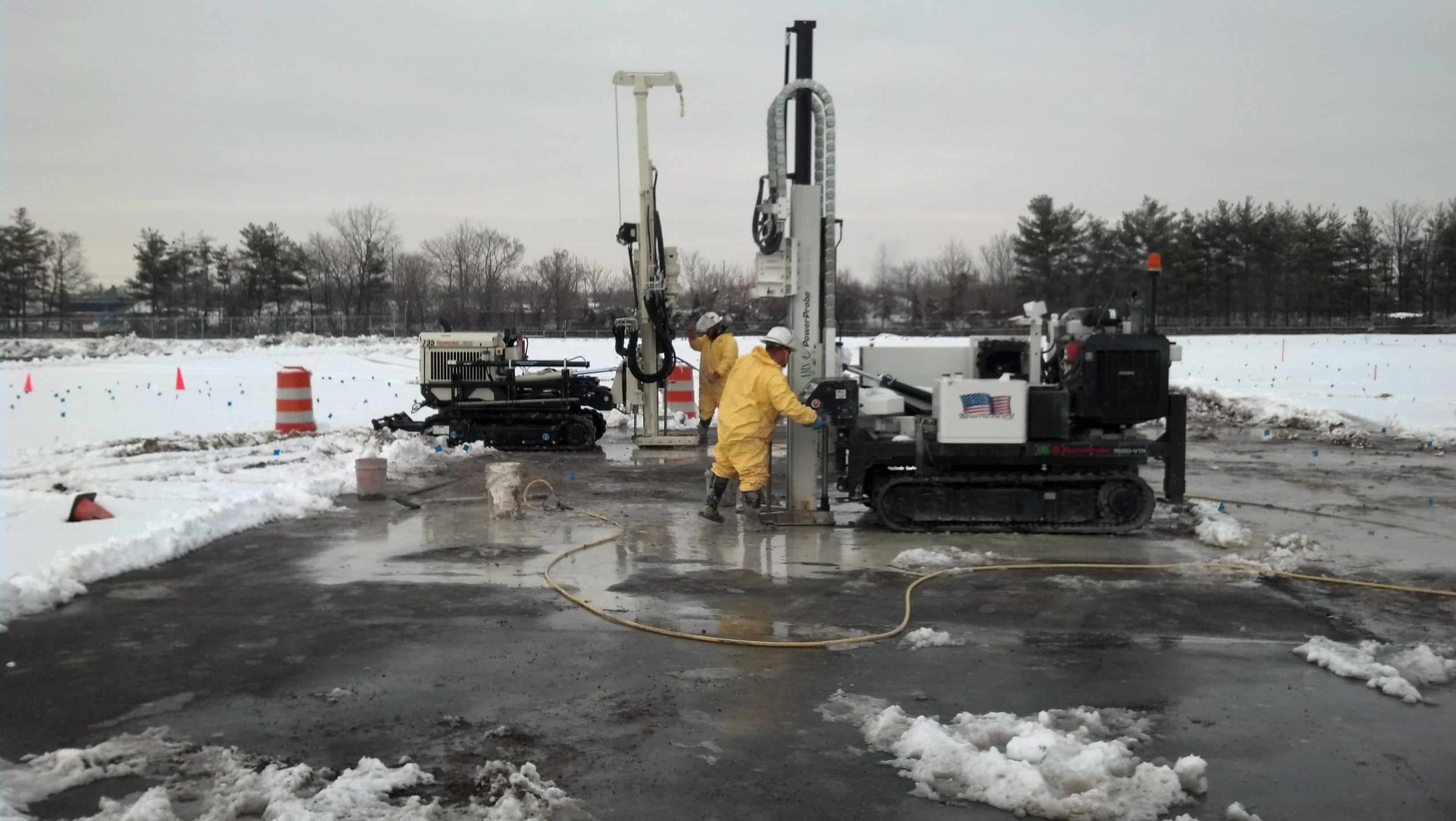
While there are many different ways to use a direct push rig, the primary way we use them at DeepEarth is to disperse our patented remediation reagent, Cool-Ox®. We use our AMS Power Probe 9500VTR DP rig to drive 1 ½ inch hollow core steel rods to the desired depth (generally just below contaminate level), and then we begin injection. This process allows us to completely saturate the contaminated soil with the reagent in a cost-effective and efficient application process at greater depths than ten to fifteen feet.
We've had decades to hone the design of our DP machine. We've even designed a process by which we can treat sites even if they have cobbles and limestone soils. Though on remedial sites with high concentrations of these materials, rotary drilling would be more feasible.
In addition, our track-mounted direct push tooling enables us to reach contaminants regardless of the site conditions. We can treat your remedial site rain, snow, or shine!
Monitoring Wells
Over the past few decades, many groundwater and soil sampling systems have been created. These systems can be used to gather data about the conditions of groundwater and soil that can then be analyzed to determine the overall presence of contaminations. One popular method is to install monitoring or recovery wells.
These wells are great for groundwater sampling, and, in addition, treatment can be administered through them. We have achieved free product destruction via pre-existing monitoring wells many times.
Whether conducting groundwater sampling, or administering remediation reagents,
DPT Injections
Once the site has been characterized, in situ bioremediation can begin. Generally, direct push machines bore tooling to the desired depths to administer the remediation reagents necessary to bring contaminant levels down to acceptable levels.
While there are several means of remediation using DPT injections, in general, these remediation reagents carry out either ISCO (in situ chemical oxidation), ISCR (in situ chemical reduction), or both, which is known as a "redox" reaction.
Either of the methods involved in a Redox reaction will alter the state of the contaminant. With a redox reaction contaminant will be reduced and oxidized until it is brought down to more acceptable levels.
Why Is Direct Push Technology Such An Effective Remediation Solution?
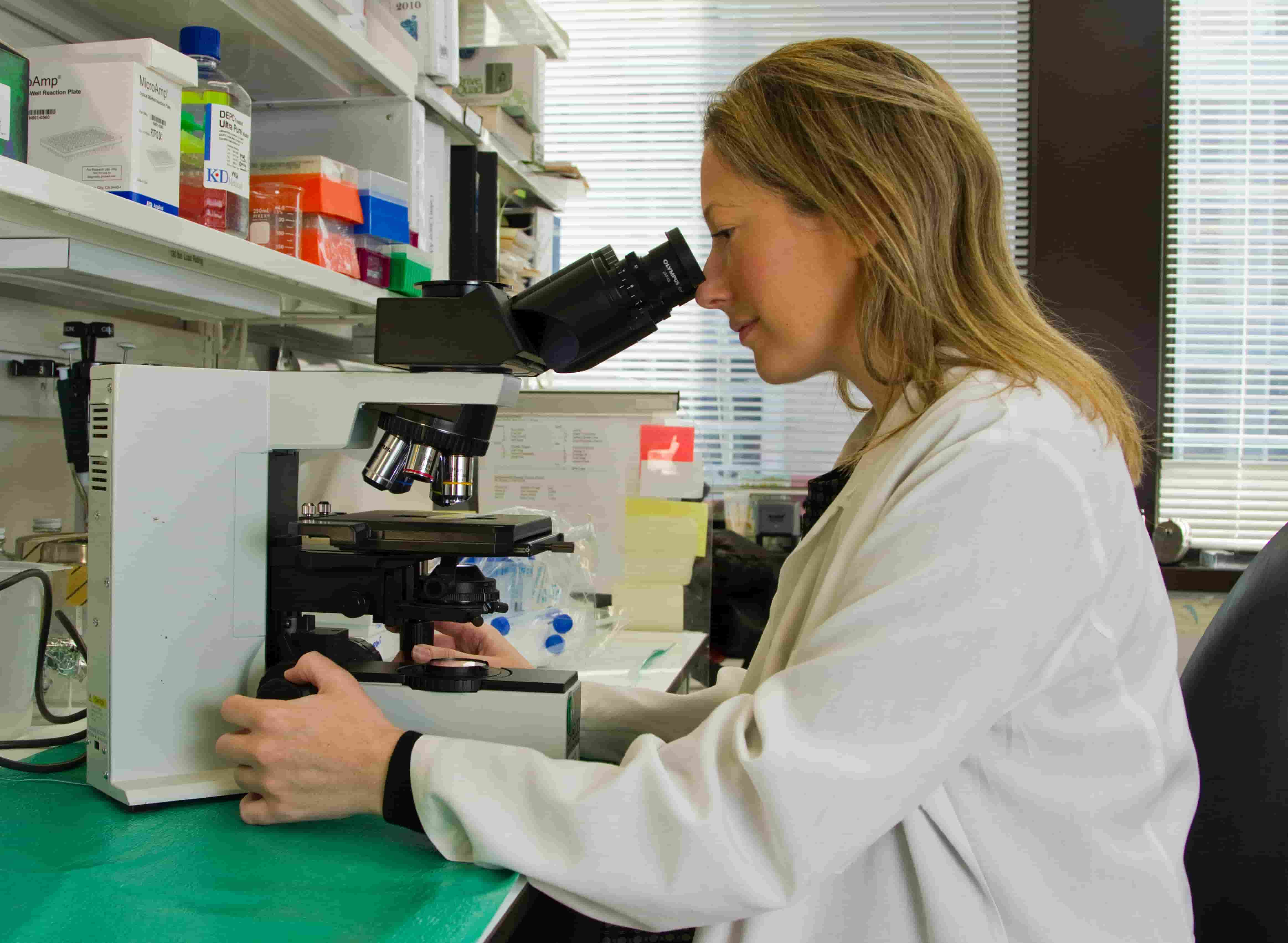
Minimal Impact
DPT Injections are one of the least disruptive ways to treat contaminated soil and groundwater. Our direct push tooling doesn't require the disruptive trenching associated with conventional drilling. It doesn't require the architecture of pump and treat, dual-phase extraction, soil/vapor extraction, or ozone oxidation systems. Our systems have a small footprint and do not interrupt or impede business during application as conventional drilling methods do. In addition to all these benefits, there is also no need to vent vapors or dispose of contaminated soil.
Save On Drill Cuttings
Our direct push tooling ensures there is no need to dispose of contaminants and there is no need to remove soil. This method pierces through the soil, meaning everything will stay in place, effectively eliminating the cost of disposing of drill cuttings. But more importantly, while using our patented Cool-Ox® reagent, the contaminant will be destroyed, even in the groundwater.
Lower Day-Rate Costs
Our team has over two decades of experience specializing in direct push technology, and we have been proven to be up to 35% faster than our competitors, meaning less time on-site and lower day-rate costs. If given the right soil type, our crew can be even faster, ensuring you spend even less.
No Direct Push Tooling Left Behind
Unlike our competitors, there is no need to leave dozens or hundreds of our rods in each injection point. Each rod is taken out before we move to the next injection point, and all that is left behind is the probe hole, which our crew will then fill.
Avoid Removing Concrete
Our DPT rig can be used at precise angles, ensuring we can treat sub-slab contaminations without the hassle of removing concrete. If this isn't possible and concrete has to be removed, minimal concrete coring will occur, and all injection points will be sealed with Bentonite®. Our team will then seal the paving with the appropriate materials.
Why Choose Us?
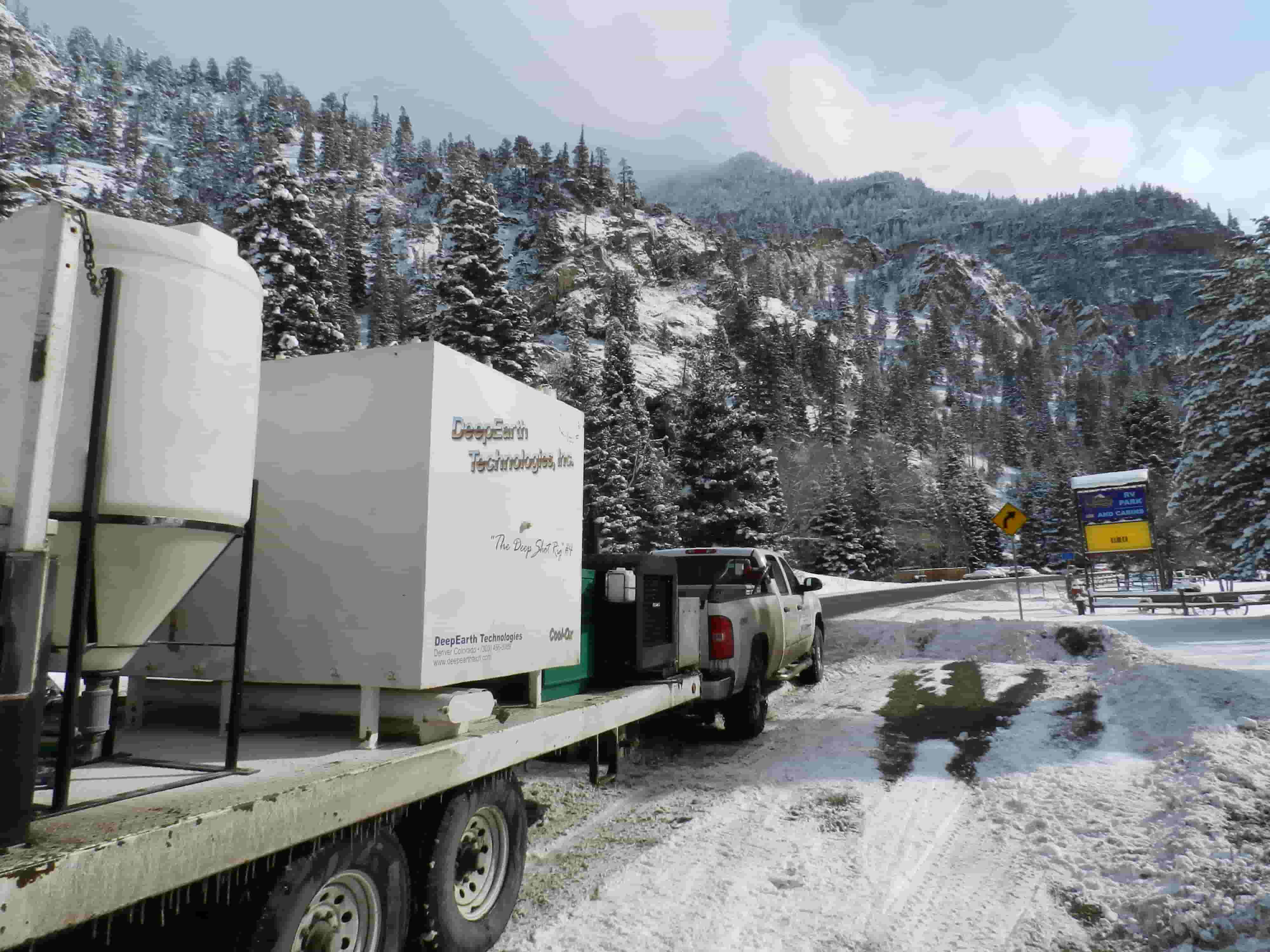
We use our patented technology Cool-Ox® in conjunction with our Deep Shot Rig to carry out all DPT applications. Unlike competing reagents, which produce unnecessary and non-sustainable byproducts and only trap the contaminant in the soil - making it likely to be disturbed and released later - it destroys the contaminants. In addition to free product destruction, our application process doesn't result in any corrosive byproducts, heat, or long-drawn-out bioremediation projects.
When you choose DeepEarth for your Environmental Remediation needs, you're using a time-tested, reliable product that promotes the growth of microbes in the soil and groundwater. Our direct push technology can close your site and promote plant life's growth in as little as 90 days post-treatment!
Our Unique Direct Push Methods
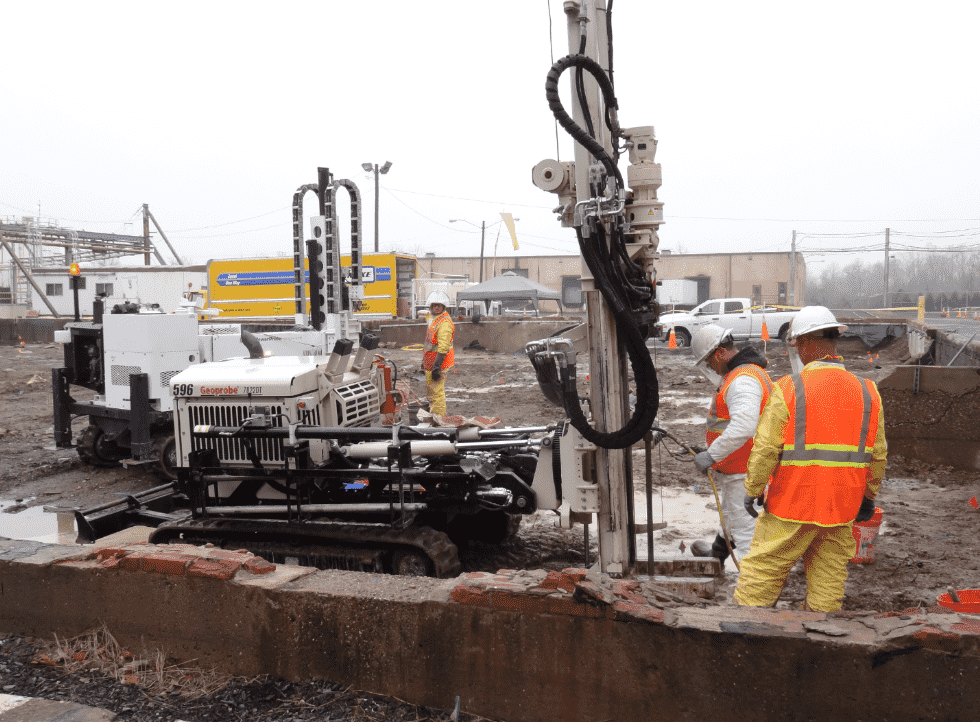
With our expertise in direct push, our patented Cool-Ox® technology, and our specialized tooling and drilling equipment, we can deliver quality environmental services to our customers. Our crews have had more than twenty years to develop drilling methods focused on efficiency, speed, and quality of service. Our drilling equipment and our tooling are made to work in nearly any soil type. Our methods are focused on transparency, quality remedial design, environmental sustainability, and, most importantly - helping our customers close their sites.
Get Your Site Back Today
If you've got a site contaminated with hydrocarbons or chlorinated solvents, MGP or brine, you can either give us a call, request a quote, or contact us with any questions to be connected to an environmental specialist.
Request A QuoteGive Us A Call